K5200xmc Plasma Cutting System
Plasma & Oxy Fuel Cutting
Bevel & Multi Torch Cutting
Drilling, Milling & More
Automated Part Removal
The K5200xmc is identical to our top-of-the-line K5000xmc plasma cutting system, but comes configured for the addition of our automated part removal system. This automated option, if included, helps shops save time by automatically removing finished parts from the machine while the system continues cutting.
Thanks to a low-profile, automated carriage, our part removal system can pick, place and palletize parts, and sort them by part, work order or batch number. It can even travel under the cutting gantry, so there is no need to stop the machine to remove parts.
- Automatically Unloads when Equipped with Optional Robot
- Sorts & Palletizes
- Plasma to 4″
- Oxy to 8″
- Boring to 8″
- High-Production Drilling to 4″
- Tapping to 2-1/16″
- Interpolated Milling to Any Diameter
- CAT 50 Spindle
- Table to 16′ Wide
This heavy-duty combination plasma cutting, oxy-fuel cutting, and milling machine will give your business a competitive edge. With multiple functions in a single machine, plus automated part removal, there’s no need for complex fixtures, multiple setups, or moving work pieces from station to station, maximizing productivity and profitability for your business.
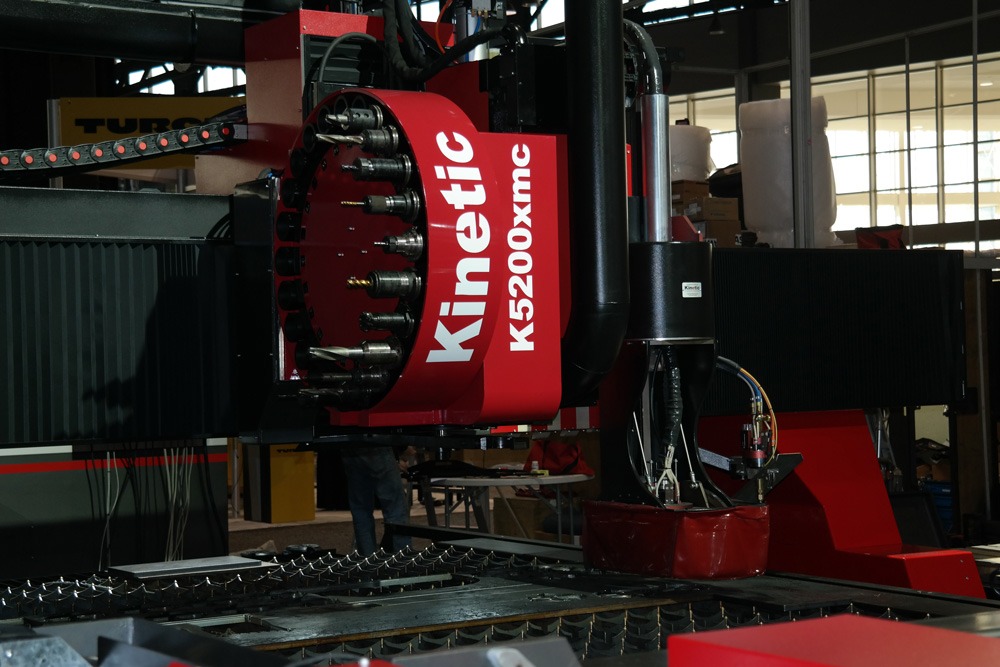
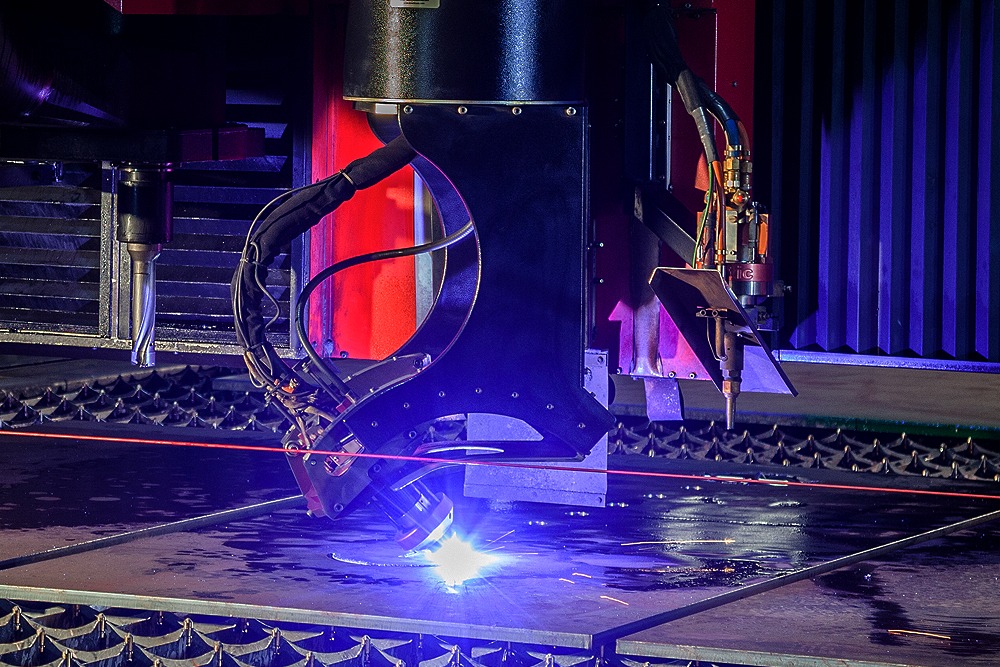
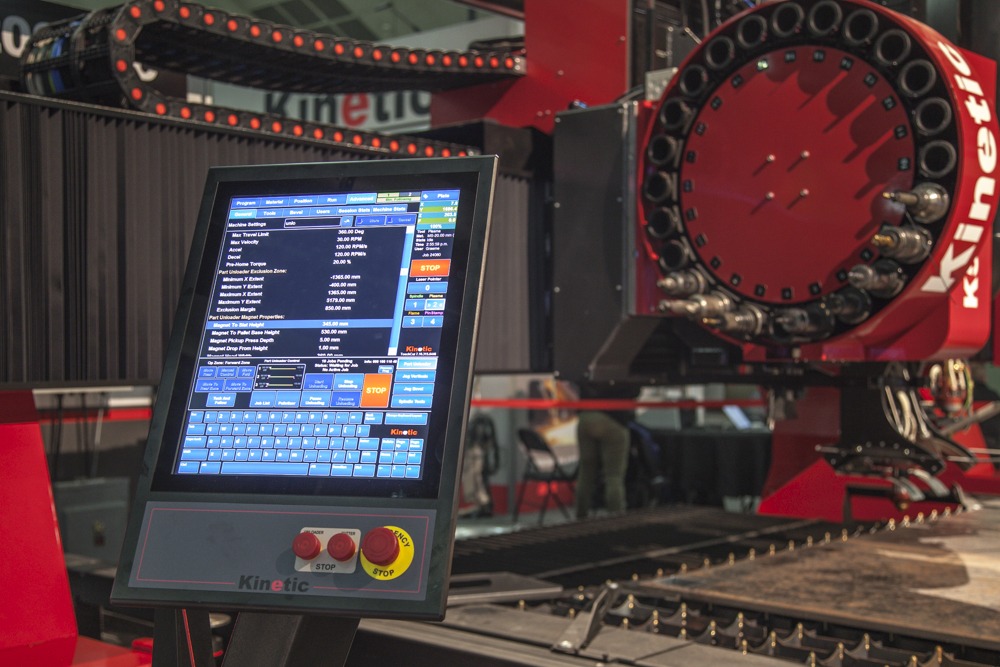
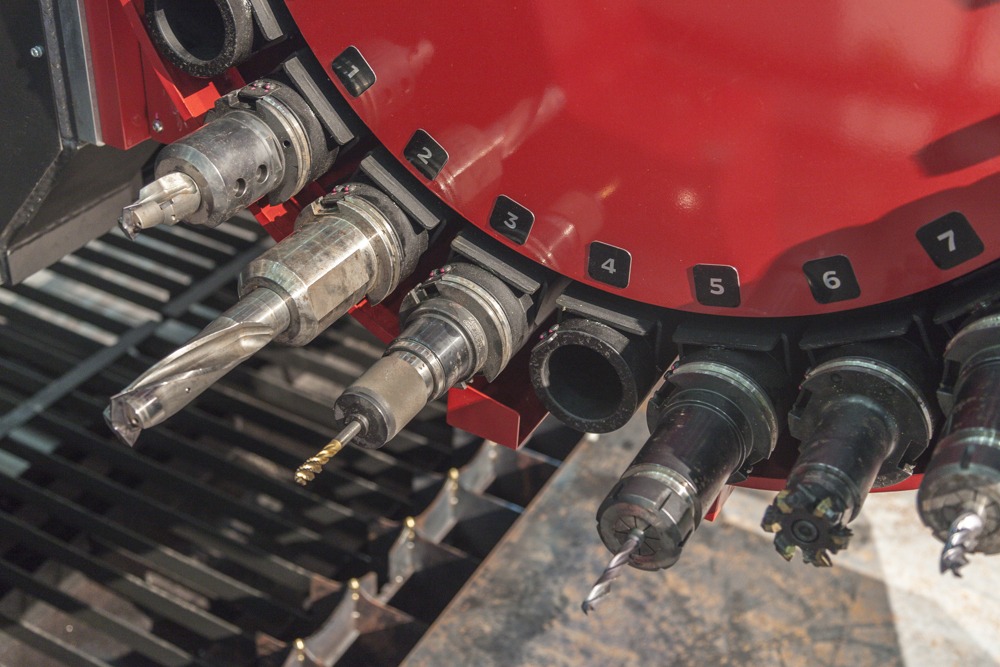
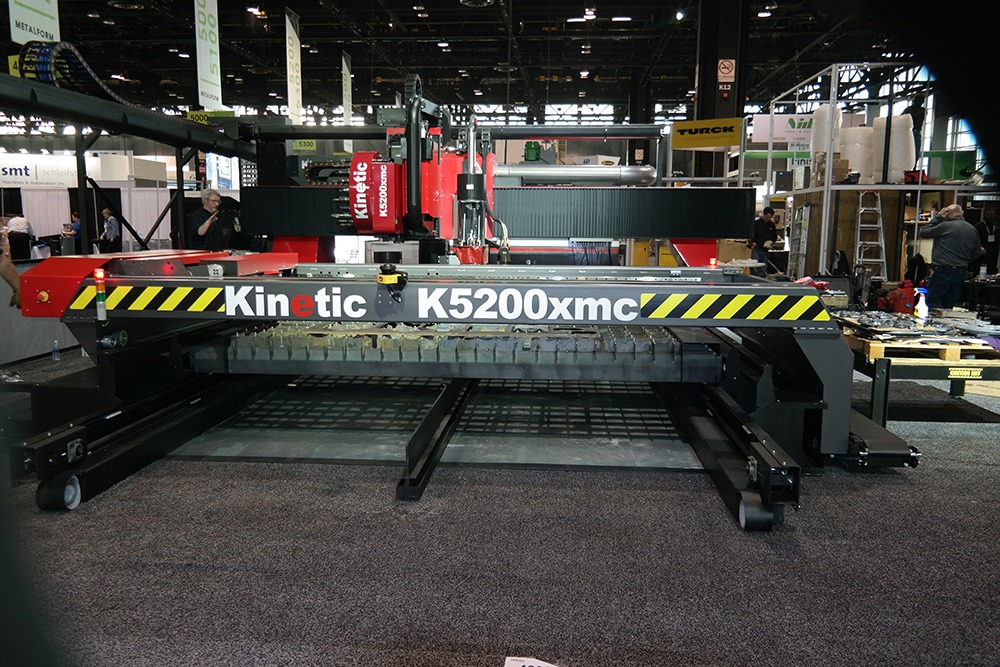
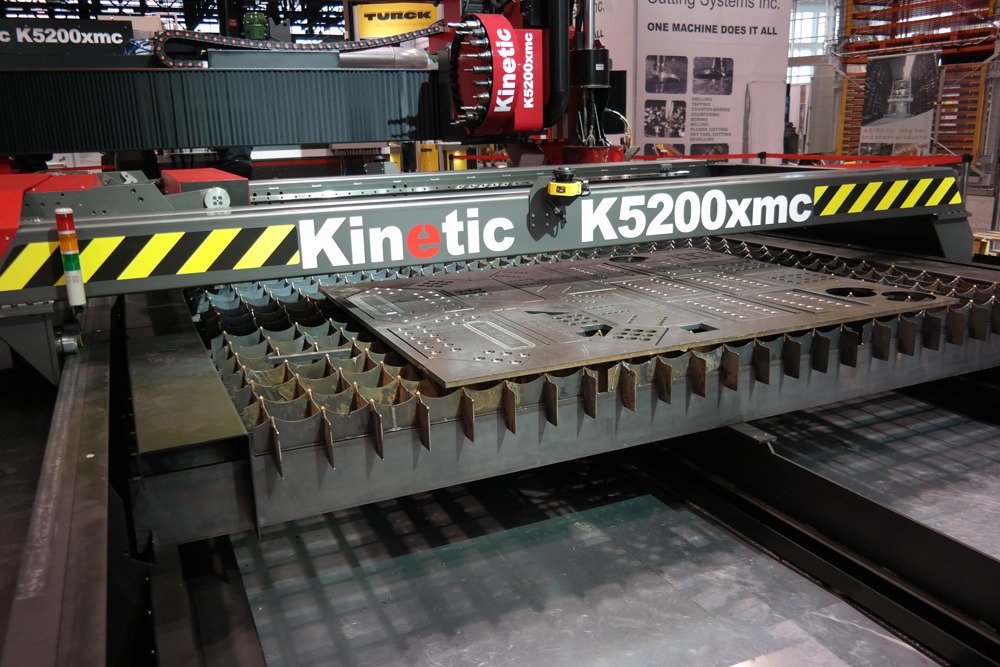
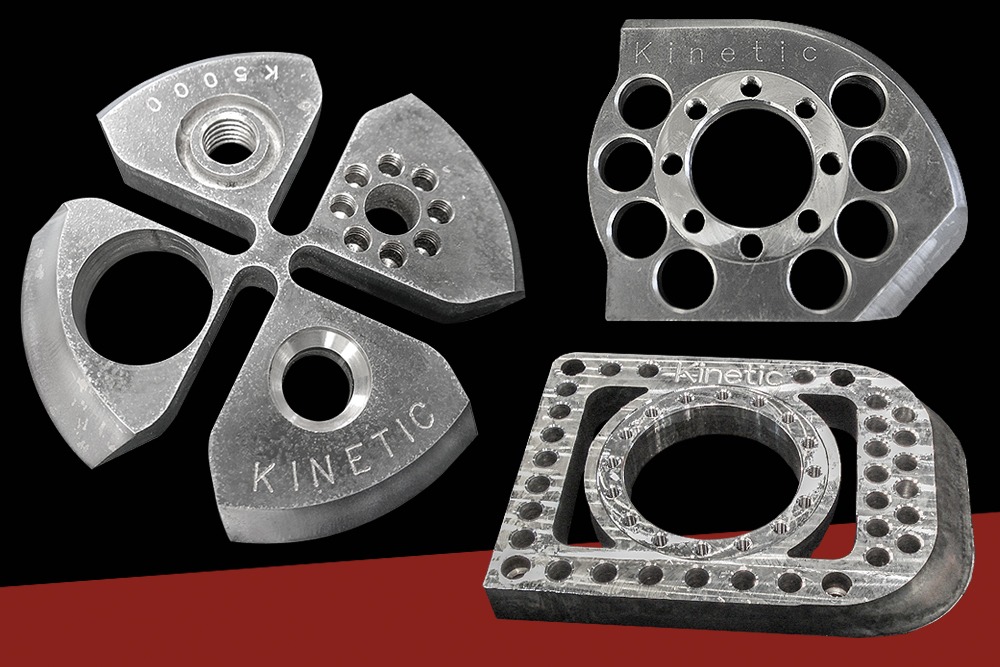
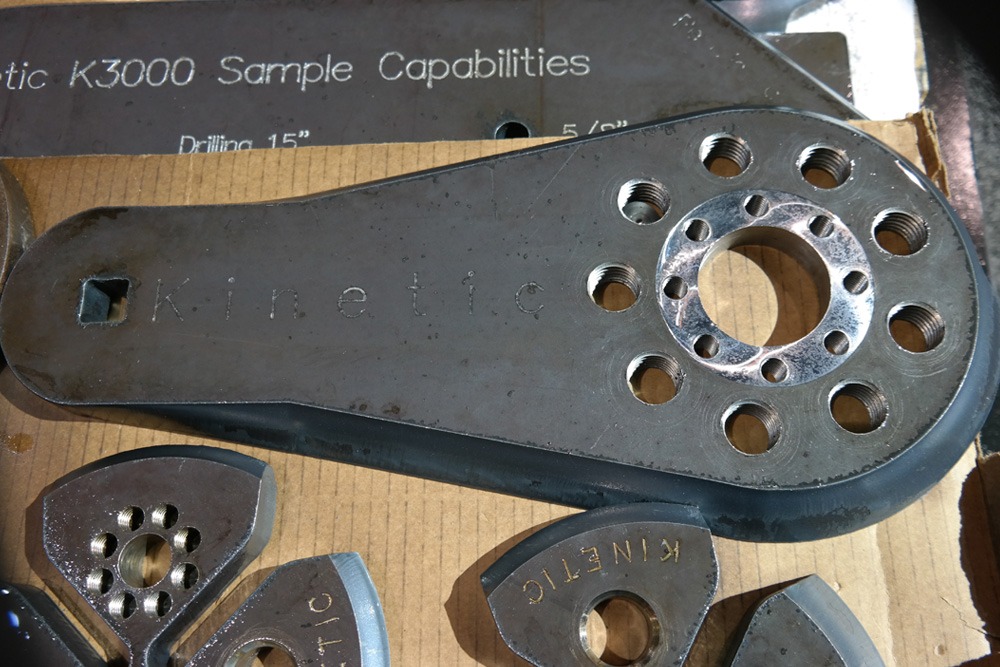
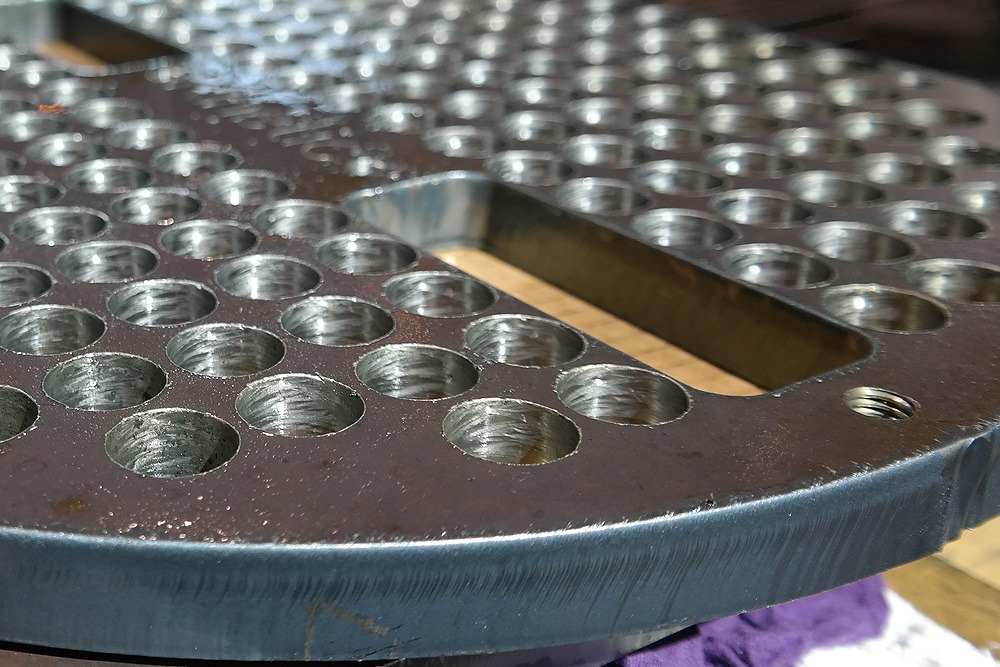
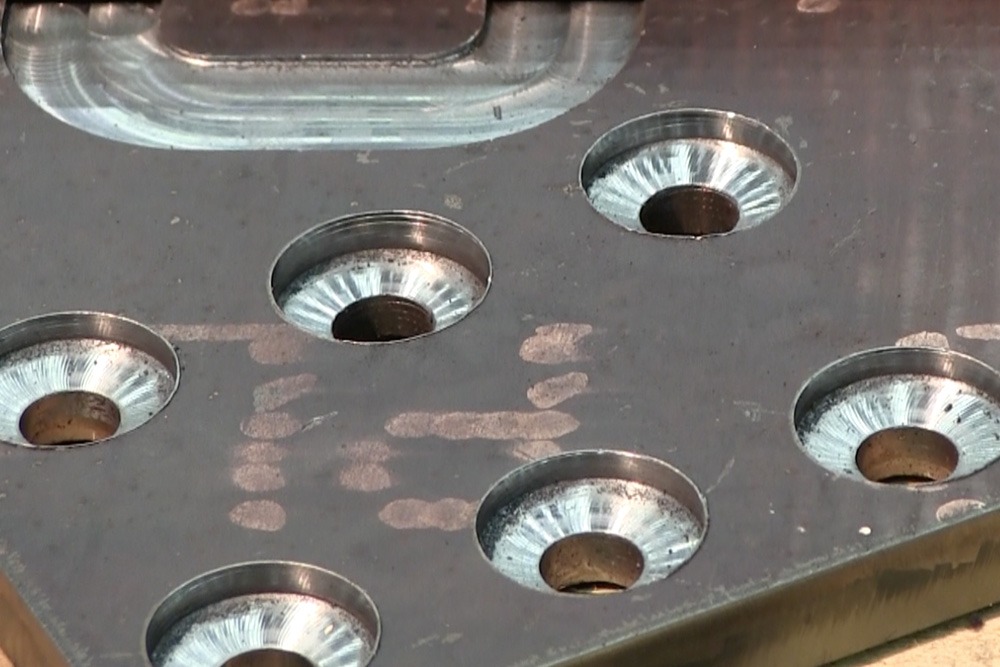
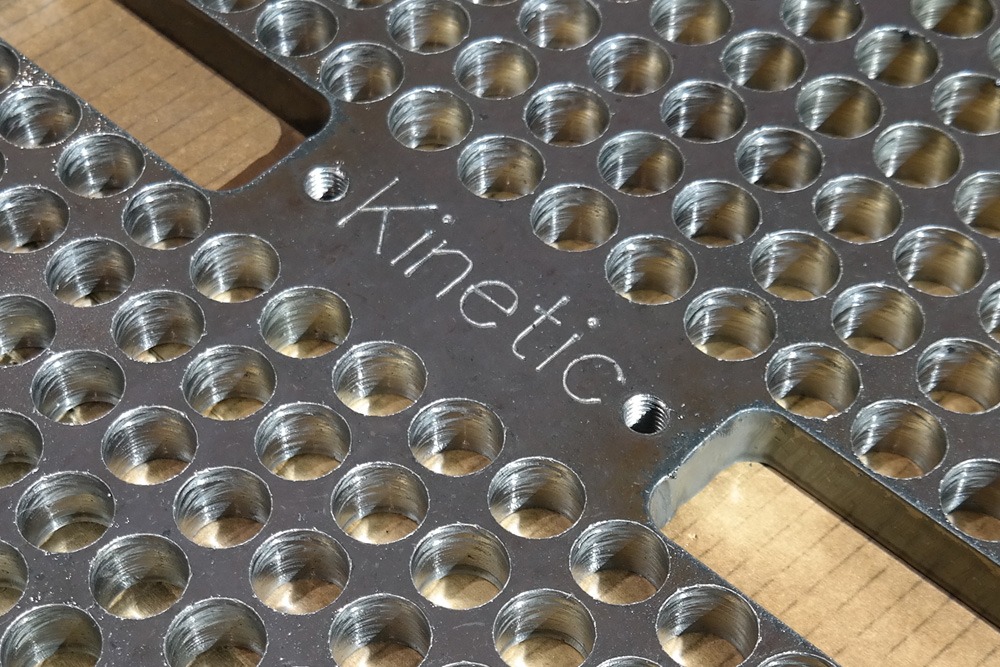
Capabilities
Cutting Capabilities
- Plasma up to 4” thick
- Oxy Fuel up to 8” thick
- Plasma Beveling
- Oxy Fuel Beveling
- Triple Oxy Beveling
- Pipe Cutting
Machining Capabilities
- High-Production Drilling up to 4” hole
- Tapping up to 2-1/16″ hole
- Boring to 8″
- Interpolated Milling to Any Diameter
- Counter Boring
- Chamfering
- Hole Interpolation
- Thread Milling
- Part Marking
Table Size
- Up to 16’ wide
- Up to 200’ long
Benefits
Maximize Productivity
- Configured for automated part removal robot for increased output
- Automatically unloads, sorts, palletizes and stacks parts
- Unloader available in 48″ or 60″ size
- Cutting, milling, drilling and more in the same step
- Multiple lifter stations for up to 2 independently driven plasma torches
- CAT 50 spindle with 24 tool stations
- Automated tool changes in under 3 seconds
- Part marking via plasma marking, percussion marking, inkjet, stamping or scribing with the spindle
Minimize Downtime
- Automated tooling alerts prevent breakdowns
- Auto tool height measurement reduces loading time
- High performance downdraft table minimizes smoke and fumes
- Innovative self-cleaning table design saves time
- Travelling dross bins for fast under-carriage cleanout
- Modular table slats for fast changeout
- Closed chip extraction system automates chip collection
- Coolant recycling system minimizes refills
- Standardized, quick-ship replacement parts
Speed & Accuracy
- Best-in-class plasma accuracy
- Best-in-class machining accuracy
- Best-in-class repeatability
- Traverse speed of 800”/min
- Dual driven rack and pinion drive system
- Linear rails with helical racking
- Programmable ball screw drives for vertical axes
- Linear bearing guide system on all axes
- 19” LCD touchscreen for fast setup and easy control
- Fiber optic network link to load programs quickly
Durability
- One-piece welded gantry designed for the rigors of modern manufacturing
- Full protection for all lines and drives
- Heavy-duty frame and component parts
- Floor mounted rails with protection
- Through-spindle coolant to extend tooling life
Options & Accessories
Options & Accessories
- Part marking via plasma marking, percussion marking, inkjet, stamping or scribing with the spindle
- Automated part removal system
- Complete customization for your specific application
Available Cutting Heads
- Hypertherm HPR800XD, for stainless steel applications
- Hypertherm HPR400XD
- Hypertherm XPR460
- Hypertherm XPR300
- Hypertherm XPR170
- Oxy Fuel cutting
- Plasma bevel cutting
- Oxy fuel bevel cutting
- Multi torch cutting
VIDEO: Part Unloader
VIDEO: K5200xmc in Action
Please note that our machine features and specifications are subject to change based on the latest engineering improvements. Contact us today with questions about specific machines and which Kinetic system will work best for your application.