PRIMECUTNE VERSION 4.5.333 RELEASE NOTES
PART-BASED UPPER BOUND ON NEST BASED MATERIAL ALLOCATION
When calculating nest-based material allocation, either for a nest based quote or for costing a nested and cut workorder, the nest based material calculation method could under certain circumstances allocate an unreasonably large area/weight of material as being used.
A nest based costing uses the following rules to determine how much material to allocate to each part, first calculating how much plate has be “used” and then how much should be allocated to each part:
PLATE USED AREA DETERMINATION
- An initial estimate for the allocated plate area is formed by one of 3 means:
- If the plate has Charge Full Plate set, then the full plate area is charged (this is the true shape area of the plate if it is a remnant or skeleton).
- Otherwise, if a crop line (not a skeleton crop) has been placed on the plate, then the area of plate used is the true shape area of the plate under the crop line. (Crop lines can thus be used to control how much plate should be charged when quoting).
- Otherwise, the area used is the area of a rectangle encompassing the extents of the nest, expanded by the plate gap.
- (New in v4.5.333) The initial area allocated is then compared to the sum of the nested part expanded rectangular areas multiplied by a factor (the global setting Max Part Rect Area Waste which defaults to 120%), and is limited to this as an upper bound.
- The resulting area is finally compared to the true shape plate area multiplied by a factor (New in v4.5.333: the global setting Full Plate Usage Threshold, which defaults to 90%. Previously this was fixed at 90%). If the allocated area exceeds this threshold, the allocated area is set equal to the true shape plate area (ie all plate is used, same as Charge Full Plate above). Note this can either increase allocated area on a plate where the computed allocated area is just less than the plate true shape area, or can decrease it when the computed area exceeds the plate true shape area.
Part Expanded Rectangular Areas
These are the areas allocated to the parts when performing a part based quote. They are computed as the extents rectangle of the parts, expanded by the plate gap (if nested on a plate, or 10mm if not), multiplied by the part’s Nest Efficiency.
Nest Efficiency
The nest efficiency is typically 110% but is settable part by part as a part property, and defaults for this value for new parts are global settings. It is intended to represent the inevitable waste introduced when nesting.
PART AREA ALLOCATION
Once the Nest area has been allocated, the parts are allocated a proportional share of this based on the ratio of their individual ship weights to the total ship weight of parts nested on the plate. This is done plate by plate, so parts nested across multiple plates may receive slightly different material allocations from plate to plate depending on how the plates are nested.
GLOBAL SETTINGS CONTROLLING NEST ALLOCATION
Two settings mentioned above are new in this version, and found on the Quote tab of Global Settings:
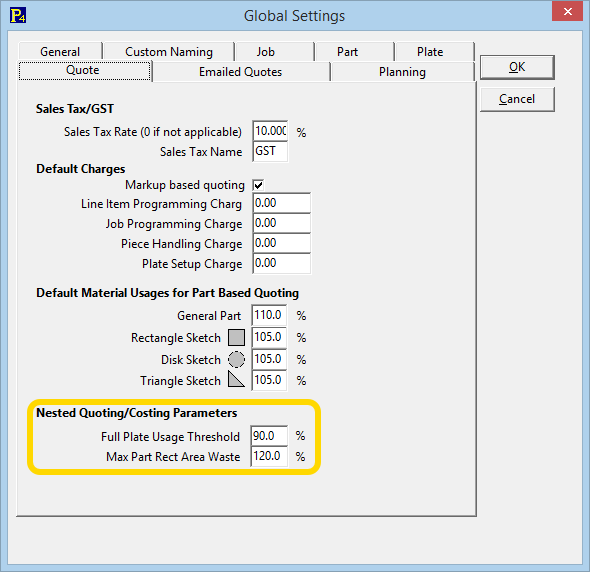
EXAMPLE OF THE MAX PART RECT AREA WASTE FILTER IN USE:
The following was nested onto a skeleton plate. The customer prefers not to use crop lines, or they could have cropped the right hand and top nested areas out of the plate, resulting in a fair nest allocation. Instead Primecut will use the nest extents rectangle, resulting in an initial allocated area greater than the plate area itself. This would then have been reduced to be exactly the plate area after determining the allocated area was greater than 90% of the plate true shape area in previous versions. The net result is that the full plate is allocated, and charged, which might be considered unfair to the customer’s whose parts have been nested in this way!
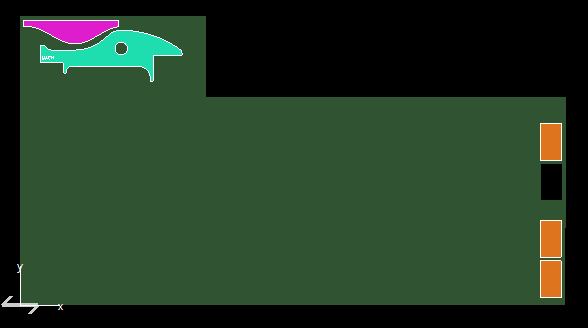
In v4.5.333 however the initial plate area is first compared to the product of
Max Part Rect Area Waste
(say 120%) and the sum of the expanded part rectangular areas. As the calculated area exceeds this (by some margin!), the allocated area is limited to it. This results in a fairer material allocation, and happier customers.
DO NOT SET MAX PART RECT AREA WASTE TOO LOW!
This filter places an upper bound on the charged material quantity, limiting it to a greater than unity (100%) factor times the area that would be allocated if a part based quote was performed. As such it acts in the end-customer’s favour only. Your efficient nesting and packing of parts can still further reduce the nest calculated charges below this upper bound to the customer’s benefit, but inefficient nesting, or parts that just don’t nest nicely, can result in material waste which the customer is not charged for, ie a loss to the cutting company. A suggested starting point is the setting default, 120%. Remember also this is applied on top of the part nest efficiency which defaults to 110%.
As it is applied at the nest allocation level, rather than the individual part level, it is still possible for individual small parts to be allocated an area much greater than expected if they are nested together with much larger parts, as the the filter works on the total area.
VISUAL ENHANCEMENTS TO QUOTE AND WORKORDER EDITING
- CUSTOMERS ARE COLOR CODED
The color setting in the customers section is now displayed editing and selecting workorders and quotes. - WORKORDER NEARLY DUE IS COLORED DIFFERENTLY
The workorder selector now only colors the Due Date column, not the whole row for clarity. The “Nearly Due” colouring (yellow) now has a settable threshold, and the threshold is workday aware, ie it takes into account weekends. The threshold defaults to the old fixed value of 2 days, however with now being work day aware, jobs due on a Monday or Tuesday will start highlighting in yellow on Thursday or Friday of the previous week.The setting controlling how many work days before due to highlight the job is set in global settings, in the Workorder/Job tab:
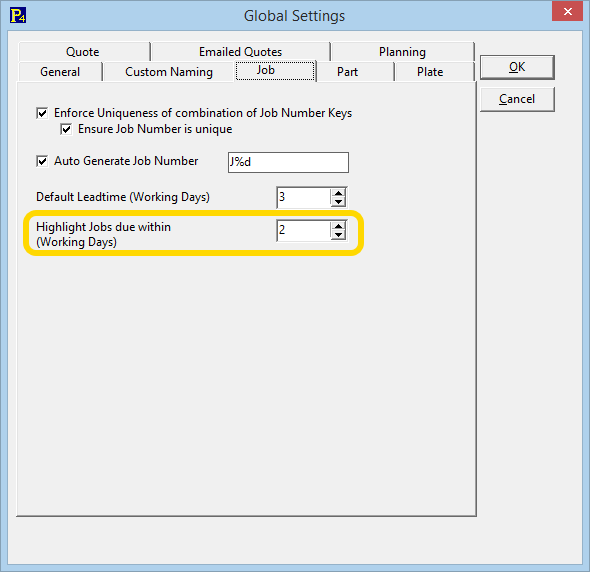
NUMBER REQUIRED IS EDITABLE IN PLACE
As it was in quoting mode.
PART REVISION REFRESH INDICATION IMPROVED.
The refresh icons have been moved into the revision number column, indications have been simplified, and the refresh icons are now clickable to refresh a single line item.
Lines with a zero quantity (often representing an older revision that must still be tracked as it is nested on plates) are now greyed out as “inactive.”
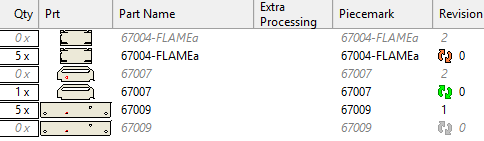
The orange refresh icon above indicates that the newest part revision is being edited in the workspace. Clicking refresh, you will be prompted to first save the workspace, including the new revision, before doing the refresh.
The lime refresh icon indicates that the latest revision exists in the database (has been saved). In this case the newer revision is already in the workorder but with quantity 0, as might happen immediately after editing a part and saving and unlocking it.
The grey icon indicates a newer revision exists, but as the quantity required is 0, it likely does not matter. This is often the case when old revisions are still tracked in a workorder after being updated – they can’t be deleted from the workorder if they exist on plates.
NEW PROGRESS COLUMN REPLACES STATUS COLUMN
Previously Primecut would indicate whether a part was partially nested, fully nested, overnested or all cut by means of ticks etc in its Status column. These have been replaced with more informative Pie Charts which are available for line items as well as for workorders. The example below is from the workorder selector showing workorder progress. This column is sortable, which should be very useful for all Primecut roles (sales, nesting, production planning etc) to quickly identify work to be done.
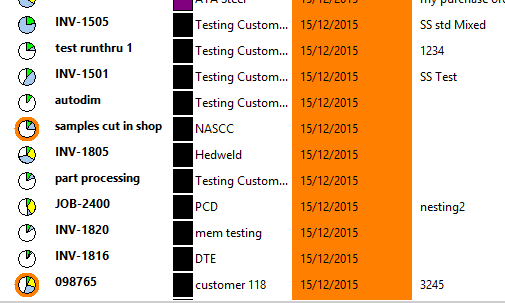
The portions of the pie chart indicate the portions of the parts required to nest (white), nested (pale blue), scheduled (yellow) and ready (lime green). An orange halo indicates one or more parts have been overnested . A red slice indicates rejected parts, for clarity this converts to a red halo around a lime circle if the workorder is ready. A green tick may be superimposed if the workorder has been closed, or a red cross if the workorder has been cancelled.
In the workorder or quote editor, each line item has a similar pie chart in the progress column and at the bottom right of screen there is an enlarged pie for the current selection of items (progress of multiple selections is combined) as well as a new, enlarged part view for single item selections. A slider to the left has been added for increasing the display row height to make the pie charts and the part icons larger.
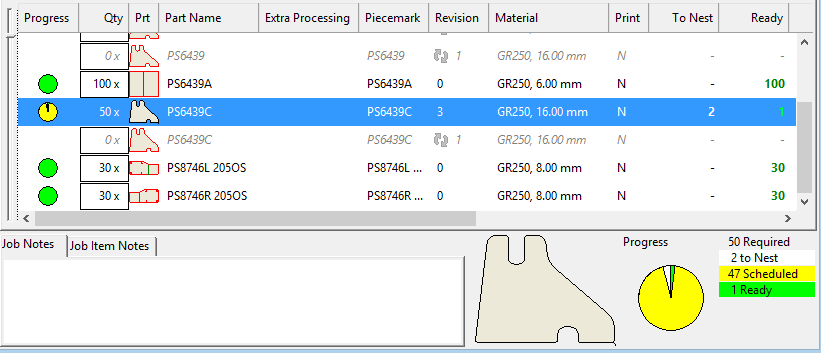
Some special cases are worth noting:
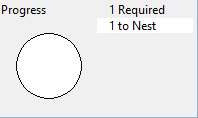
White circle: No parts nested yet.
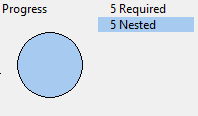
Blue solid circle: All Parts are nested, none are yet scheduled.
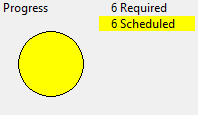
Yellow solid circle: All Parts are nested and scheduled.
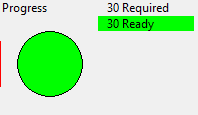
Lime solid circle: All parts are ready.
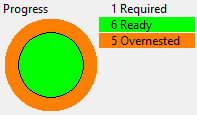
Lime solid circle with orange halo: all parts are ready but overnested.
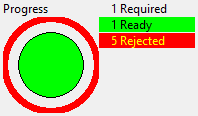
Lime solid circle with red halo: all parts ready, some rejected (6 cut in this example).